Dynafoam® Foam-In-Place Gasketing
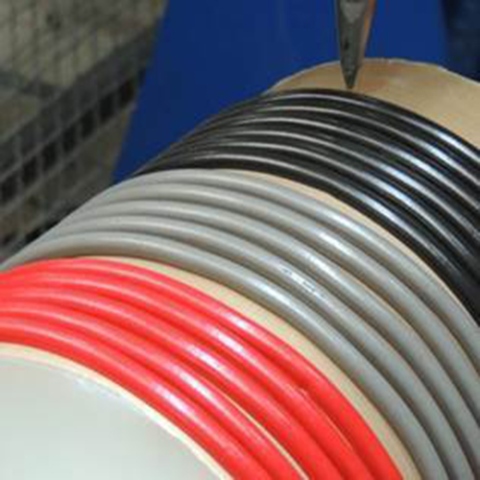
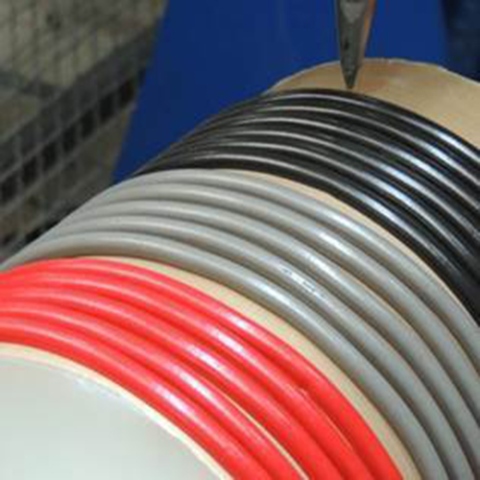
Specification
Dynafoam Foam-In-Place Gasketing (FIPG) technology is based on mono-component Polyurethane (PUR) chemistry.
Dynafoam products are physically foamed by injecting Nitrogen (N2) and curing takes place once the product is out of the foaming system in contact simply with the humidity of ambient air or under accelerated humidity and temperature conditions.
Because Dynafoam products are mono-component; there is no need for metering different chemicals, no need for mixing reactive chemicals close to the dispensing gun and no need of purging material during production cycle, even for long breaks, eliminating waste that harms the environment and the cost.
Overview:
The product is shipped and stored in multilayer moisture tight sealed bags contained in 20 liters pails or 200 liters drums. The drum unloader plate of the foaming system is directly pumping the material from the bag avoiding all contact of materials with ambient air.
Saint-Gobain’s advanced patented FIPG technology offers high process reliability, saving cost by eliminating variances under large environmental and production conditions without operator intervention. Unlike 2 components PUR, there is no need to neither change equipment settings between very large variations of atmospheric conditions nor condition the parts at room temperature before gasketing operation.
Thanks to their thixotropic behavior, Dynafoam products can be applied on 3 dimensions. This enables the gasket application in any direction (even upside down) without any limitation allowing easy part handling during and after gasket application. Depending on the automation, it allows the robot to handle the part instead of the dispensing gun, creating important savings on part transfer and handling.
When applying Dynafoam gaskets on injection molded plastic parts, it is common that the same robot discharges the part from the mold, cleans the injection gate, applies the Dynafoam gasket and packs the part immediately after the gasket application.
Features:
• Replaces the difficult and expensive manual application of gaskets
• Enables complex 2-D and 3-D sealing designs
• Provides design freedom in terms of gasket shapes and cross sections as well as substrate interfaces
• Allows for mechanically and chemically robust gaskets
• Provides excellent adhesion to a wide range of substrates
• Very low free iso-cyanates
• Solvent free